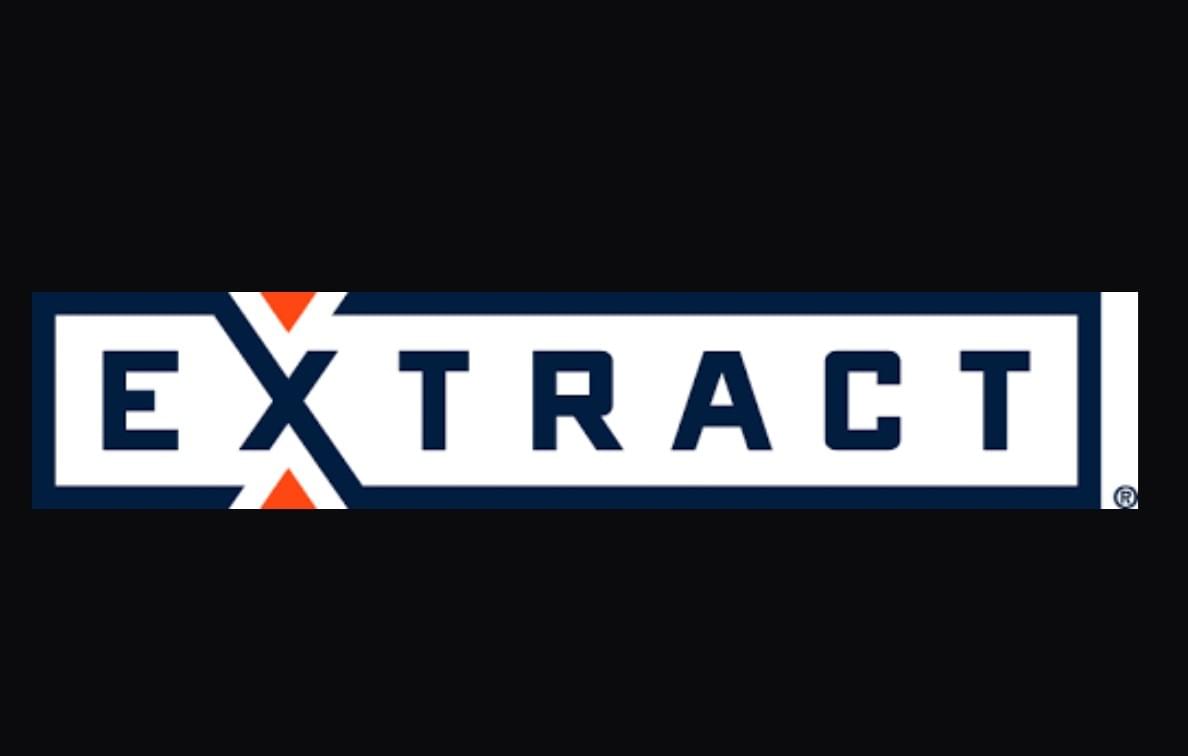
Maximum production and system durability are essential for ESP and horizontal pumping systems. Pump maintenance improves performance and profitability in oil and gas, water treatment, and other industries. One of the best techniques is responsive service. Learn more about artificial lift oil and gas
Understanding Horizontal and ESP Pumping Systems
Electrical Submersible Pumps (ESPs) are vital in oil extraction since they pump fluids from deep wells. Regular maintenance is necessary since these systems manage high pressures and diverse conditions. However, horizontal pumping systems are employed for wastewater treatment and long-distance liquid transport. Two systems are essential for seamless functioning in harsh conditions.
Why responsive service matters
Responsive service addresses pumping system needs proactively. It requires timely problem identification, repair implementation, and performance monitoring to avoid significant failures. Problems have less influence on production if addressed quickly. How timely service may boost ESP and horizontal pumping system value:
Low Downtime: Regular maintenance and repairs prevent unexpected malfunctions and maximize system performance.
Cost Efficiency: Early detection prevents costly repairs and replacements.
Extended System Life: Regular monitoring and quick adjustments extend ESP and horizontal pump lifespans, maximizing your initial investment.
Optimized output: System efficiency helps you sustain high output, reducing delays and inefficiencies.
Best Practices for Value Maximization
These measures can boost the value of your ESP and horizontal pumping systems:
Inspections: Schedule regular inspections to spot faults before they become problems.
Training for Operators: Proper training helps your team understand the systems' needs and spot wear and malfunction.
Decisions Based on Data: Monitor pump performance and modify using real-time data.
Q1: How often should I service my ESP system?
A1: Maintenance should be done every 3-6 months, depending on environment and system use. If performance drops or energy consumption rises, more regular inspections may be needed.
Q2: What causes horizontal pump failure?
A2: Wear, clogging, misalignment, and seal or bearing failure are common failure causes. These concerns are caught early by regular maintenance.
Q3: How can responsive service boost system efficiency?
A3: Because proactive service fixes issues promptly, reduces downtime, and optimizes system efficiency, your pumps function efficiently and boost productivity.
Conclusion
ESP and horizontal pumping system maintenance must include prompt service to increase value. Preventative maintenance, quick problem resolution, and continual optimization can boost production, increase system longevity, and cut downtime and repair costs. Prioritizing quick service will maximize system performance and ROI.